For decades ERP Software vendors have been claiming to possess an almost-magical ability to reduce your MRO costs by structuring your data. Well, they were wrong. They could not, cannot, and most likely never be able to do that. No shortage of pretence though, just a spectacular lack of content.
Why is that?
MRO data is extremely divers. But that doesn’t make the characteristics of the parts any less relevant. For example, all the information that you need in order to correctly identify a simple bolt is useless when it comes to identifying a sensor or a ball bearing. But all of these are typical spare parts that almost everyone uses. Compare that to the data you need to store for a debtor or a creditor in the system, which is fairly uniform across the world, and the problem becomes quite clear. An ERP system is a bookkeeping software on steroids, but in the case of MRO data, size actually doesn’t matter.
The obvious first problem that needs to be tackled is the diversity of the data. This requires quite a flexible solution; something that an ERP system simply can’t offer. The second issue is that similar to the meaning of the word “success”, MRO data means different things to different people (or in this case, departments). Procurement officers don’t worry about the dangers of having the wrong bolt in stock; cost and speedy delivery will be on the top of their list. On the other hand, your Maintenance department may agree on the speed issue, but what they really need is enough technical data in order to be able to identify this spare part as the correct one. By the time you reach the Logistics department, they are already thinking about the packaging size, weight and special requirements. And while all of this is happening, Finance is fuming about invoice reconciliation of the actual deliveries, “…no partial deliveries please, and no messing around with packaging of price units!”.
On top of all of that complexity and the fact that data is not uniform (standardized), you also have to factor in all of the non-technical product data that these departments have attached to the parts. In fact, depending on the size of the organization, it may be necessary to store hundreds of attributes to a “simple” screw, just so each department has the necessary information. And imagine how many you need once you reach the motion sensors… And don’t forget that the data should be displayed to the right people at the right time. After all, maintenance should be easy and product creation should be rapid. Otherwise you are losing competitiveness.
Tell me again, how all of this can be done by an ERP system?
A pebble in your shoe
Now, I know what you are thinking. If this problem is so urgent and obvious, why has nothing been done about it?
The simple truth is that every department is suffering but none of them to a “lethal” degree. It’s like having a pebble in your shoe when you are in a hurry. It’s just a pebble, you can tolerate it, right? Besides, you don’t have time now to stop and take off your shoes to get it out. What harm can it do anyway? This is more or less how everyone deals with the issue. Everyone just finds a way around the problem.
When sizing the scale of a client’s MRO problem, I always tell them, “Don’t show me your ERP system, show me the Excel sheet and your Access tools.” Once you take a look at those, you really find out how their ERP system has failed them. One time I had a client with more than 9,000 Access tools. All of those were ad hoc product data solutions. Quite the pebble if you ask me.
Besides the obvious control and standardization issues, the problem with all of those Excel and Access solutions is that they are always on local devices or personal accounts. Even if it is something used by the whole department, it’s rarely shared with the rest of the company. Which means that things never get fixed. All of this leads to what I call “the Circle of Misery”. A never-ending sequence of “pass the pebble to the next shoe” where everyone is working hard to fix their own problem but unknowingly messes it up for the next link in the chain. Typically, it looks something like this:
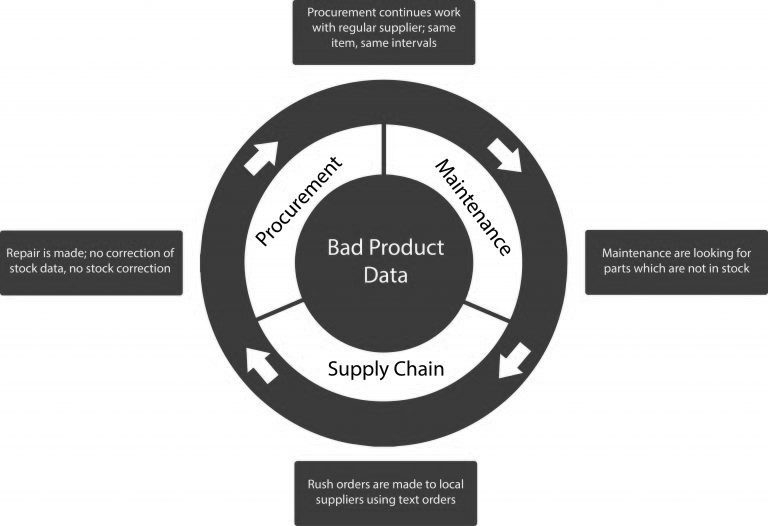
So, why is this not the next priority at the boardroom meetings? Well, a typical manufacturing company will spend anywhere between 2% to 6% of their budget on MRO. At first glance there is little to be gained from improving your MRO data and processes. Even if you are optimistic you may be able to report a 1-2% of savings. Hardly convincing. Especially if solving the problem is more trouble than it’s worth.
However, while MRO spend is relatively small, the impact is much larger than what is reflected in those numbers. Operational disturbances because of MRO-related issues are costing companies around the world a lot more than what they report is being spent on MRO. Think of machine downtime because the right part is not there, or even worse, it’s there but nobody knows its name. Or, if you are a supply chain manager, consider this, how many of your suppliers can be removed if you only knew the optimum amount of parts and where you can get them from? Better to have 300 suppliers than a 1000, no? The tendency to find workarounds to those problems also leads to a lot of wasted time and work, often duplicated across departments. As the saying goes, “It isn’t the mountains ahead to climb that wears you out; it’s the pebble in your shoe.”
So, are you ready to take back control?