The Challenge
Our client faced a significant challenge in making their extensive spare parts inventory management more effective. Over the last two decades, approximately 200’000 (out of over half a million) materials with incomplete meta-data have accumulated in their database and become a legacy with regards to the planned upgrade from SAP R/3 to SAP S/4 HANA. Although orders and storage had been carried out, fragmented, incomplete, and inconsistent data led to considerable difficulties, such as:
- Inconsistent supplier data made it difficult to reorder missing components
- The assignment of spare parts to specific vehicles, coaches, or components was unclear
In light of the planned system upgrade, it became evident that data quality and completeness urgently needed improvement to ensure a smooth transition.
The Approach
To address these challenges, Eraneos experts collaborated with the client to implement a proof-of-concept (PoC) Data Unity solution. Our approach focused on enhancing data quality and identifying similar records within their extensive parts inventory.
The project began with in-depth discussions with the relevant stakeholders within the company in order to understand their specific needs and the scope of the data issues they faced. The client provided a sample data set in several Excel sheets containing detailed records of spare parts, their descriptions, dimensions, and other relevant attributes. These initial inputs were used to design a robust data ingestion pipeline.
Given the complexity and volume of the data, we used Databricks on an Azure environment to store, process and transform the data. This choice of platform allows us to handle large datasets in a scalable, efficient manner. We ingested the data into Databricks tables, leveraging its robust capabilities for large-scale data processing.
With a clearer understanding of their inventory, the client can streamline their processes for locating and ordering parts, reduce the time and effort required for maintenance operations and increase operational efficiency.
Data Unity
The core of the Data Unity solution is a smart matching engine capable of identifying similar parts and enhancing data quality. Implementing this solution involved feature engineering, creating embeddings from the textual data and implementing algorithms to identify and match similar items within the dataset. The smart matching engine is capable of identifying potential suppliers for parts and determining which parts belong to which trains or components. Furthermore, similarity algorithms were implemented to identify parts that were likely the same or interchangeable, including semantic similarity and dimensional analysis. Supplier matching was also conducted by analyzing similar parts and their known suppliers to fill in missing supplier information.
To provide the client with actionable insights, we initially developed graph visualizations to illustrate the relationships and clusters of similar parts, supporting the explanation of the system during the project presentation. However, based on the client’s feedback, we subsequently focused on delivering detailed tables that provided a clear and practical format for analyzing the results. These tables were tailored to the client’s specific needs, offering a more user-friendly and actionable representation of the data for operational use.
Our client is a European national railway company. They are responsible for transporting more than one million passenger per day and employ more than 30,000 people.
The Results
Our Data Unity solution shows potential for fully streamlining the client’s spare parts management. The smart matching engine provides reliable recommendations for supplier identification. The matching to the right trains and components didn’t provide reliable recommendations because similar articles do not indicate whether the corresponding article is installed in the train.
Nevertheless, Data Unity can help to find duplicates, optimize purchase prices and thus optimize the supply chain. With a clearer understanding of their inventory, the client can streamline their processes for locating and ordering parts, reduce the time and effort required for maintenance operations and increase operational efficiency. By improving data quality and completeness, the project also helped lay the groundwork for the client’s migration to a new SAP system.
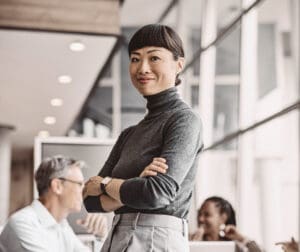