In an era of unparalleled uncertainty and risk, European businesses across various sectors face many challenges. How can organizations adapt, evolve, and thrive as the world experiences rapid shifts in the geopolitical and economic landscape? This question is at the heart of our Brilliance in Resilience blog series. In this second instalment, we explore the critical disruptions that have shaken the manufacturing sector and discuss the strategies needed to build organizational resilience in this volatile environment.
The unfolding crisis in manufacturing
Once the cornerstone of many economies, the manufacturing industry has declined over the past four decades. Data from the UN and World Bank highlight this trend, with Germany’s manufacturing contribution to GDP shrinking from 33% in 1980 to just 18.96 % by 2023. While the sector was already contending with these challenges, recent global crises—including the pandemic, the Russo-Ukrainian war, and Europe’s energy crisis—have magnified these disruptions. These events have triggered severe issues, from supply bottlenecks to skyrocketing costs, leaving many manufacturers struggling to stay afloat.
Six big disruptions in the manufacturing industry
Below are the six most pressing disruptions currently impacting the manufacturing industry:
1. Labour shortages
The manufacturing sector is facing a critical talent shortage. A 2023 survey by ManpowerGroup revealed that 75% of employers across 21 European countries struggled to find workers with the right skills, a significant increase from 42% in 2018. This shortage is especially acute in sectors requiring advanced technical skills, which many older workers lack. As new technologies reshape the manufacturing industry, companies are increasingly pressured to attract younger, digitally-savvy talent while upskilling their existing workforce. This widening skills gap poses big challenges for manufacturers trying to maintain a competitive edge.
2. Material shortages
Material shortages have plagued the manufacturing sector, with supply chains severely disrupted by geopolitical tensions, such as the war in Ukraine and trade dependencies on Russia and China. The situation slightly worsened in 2024, with 14.6% of German manufacturing companies reporting shortages of raw materials and intermediate products, up from 12.5% earlier in the year. Supply chain disruptions are particularly acute in sectors such as automotive, chemicals, and electronics, with some industries reporting shortages as high as 57%. Moreover, Europe’s growing dependence on imports from China (€472 billion in 2022) raises concerns about further shortages if conflicts arise between China and Taiwan.
3. Demand surges
The lifting of Covid-related restrictions triggered a surge in demand across multiple industries. However, this resurgence exacerbated existing imbalances between supply and demand. Manufacturers have been caught in a bind—struggling to ramp up production fast enough to meet the unexpected spikes in demand, all while navigating ongoing supply chain issues.
4. Offshoring disruptions
The pandemic exposed the vulnerabilities of offshoring strategies, as lockdowns, natural disasters, and geopolitical tensions disrupted global operations. As a result, many corporations are rethinking their reliance on offshored manufacturing. The CEO of a major manufacturer shared a vivid example:
“Earlier this year, our factory in China was shut down completely for two weeks due to a citywide Covid lockdown in Suzhou. We received no early warning—it happened overnight.”
This unpredictability has pushed many companies to explore reshoring as a more stable alternative.
5. Cybersecurity threats
As technology continues infiltrating every aspect of manufacturing, companies are increasingly vulnerable to cyberattacks. In 2024, Check Point reported that the manufacturing sector experienced an average of 1,636 weekly cyberattacks, marking a 30% year-over-year increase and ranking it among the top ten most targeted industries. Protecting against these threats requires robust cybersecurity measures to safeguard data, systems, and supply chains from disruption.
6. Increased costs
The above disruptions have contributed to a sharp rise in manufacturing costs. Geopolitical events, increasing labour cost to compensate current inflation, climate change impacts, and soaring energy prices drive operational costs to unsustainable levels. Many manufacturers, such as France’s Arc International, face tough choices. As their CEO put it:
“This is the most dramatic situation we’ve ever encountered. We don’t want to stop operations completely but will not produce if we lose money.”
The struggle to balance escalating costs while maintaining operations is critical for European manufacturers.
Building resilience: what’s next?
To navigate these turbulent times, manufacturers must adopt a dual defensive and offensive strategies approach. Defensive tactics might include shoring supply chains by diversifying suppliers and investing in cybersecurity. An offensive strategy could focus on innovation, such as adopting advanced technologies to streamline production and reduce reliance on vulnerable global supply chains. As we explore resilience in future blogs, we’ll discover what is needed for overcoming these challenges and positioning your organization to survive and thrive in the face of disruption.
Get in touch
Stay ahead of the curve! Read our next blog Part 3 in the Brilliance in Resilience series, where we will explore how organizations can navigate talent market challenges and build resilience in a competitive landscape.
<- back to Part 1
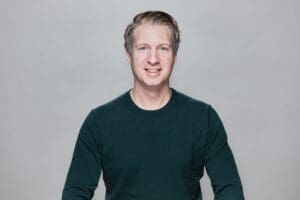
Koen Boomsma
Senior Manager – Organizational Excellence & Transformation
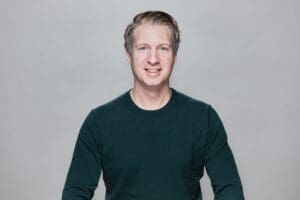
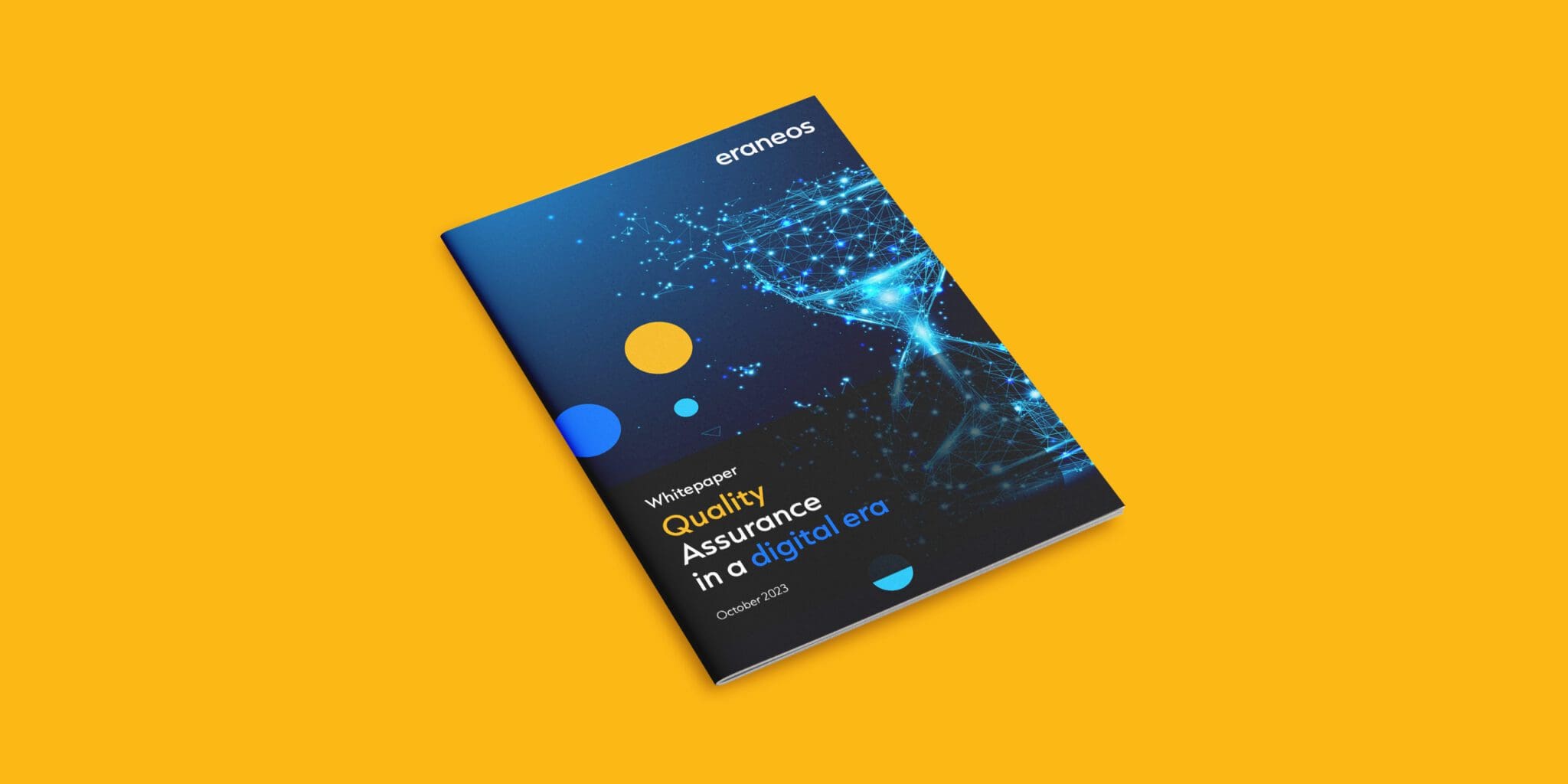
Quality Assurance in a digital era
So, what is the impact of this digital transformation on the Quality Assurance field of expertise? What is this shift towards ‘built-in’ in the field of Quality Assurance? What does this mean for these three lines of defense? In short: The answer is Exponential. Let us explain it to you in this whitepaper.
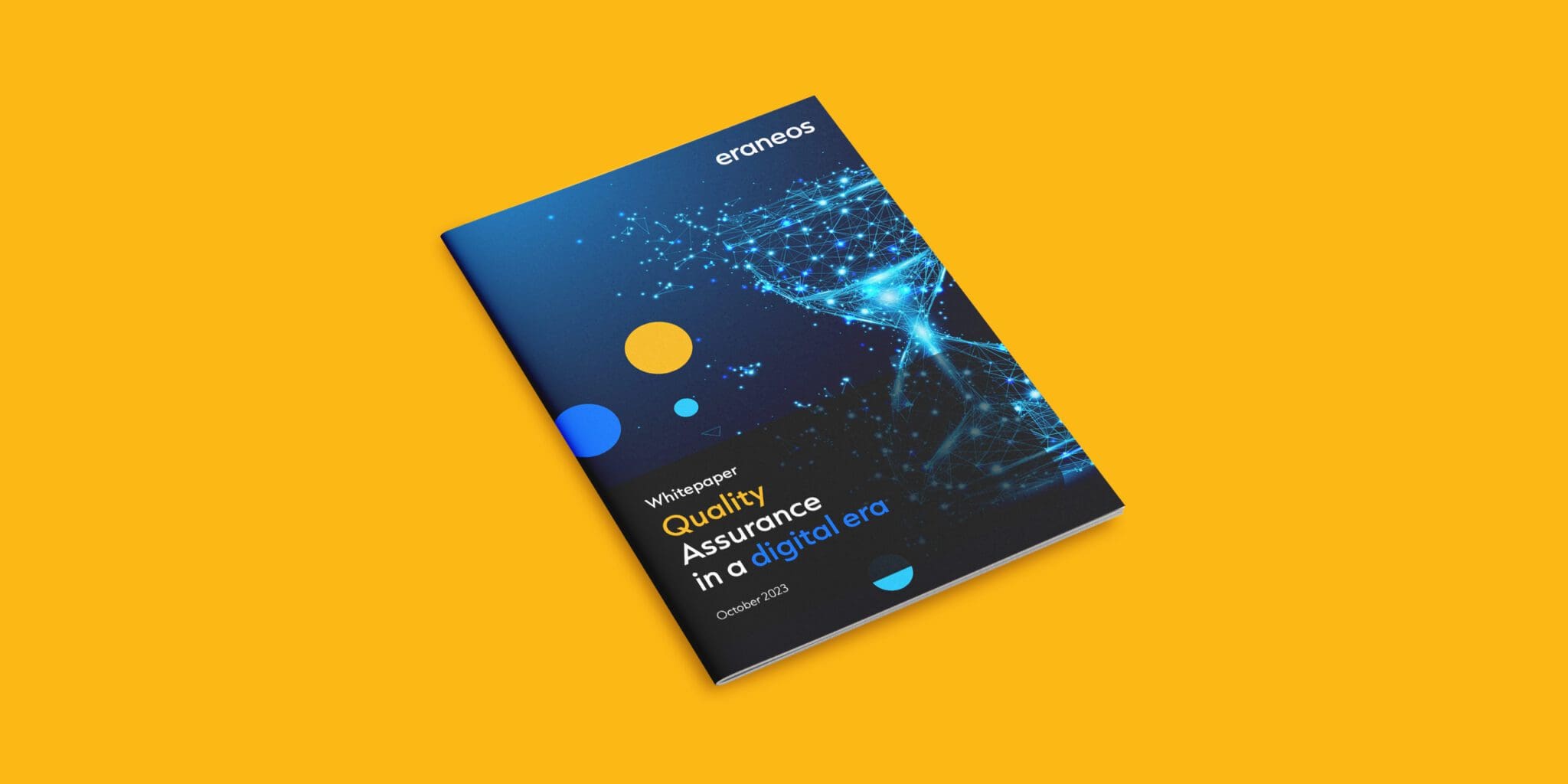